Why has the cost of steel and aluminium changed so much?
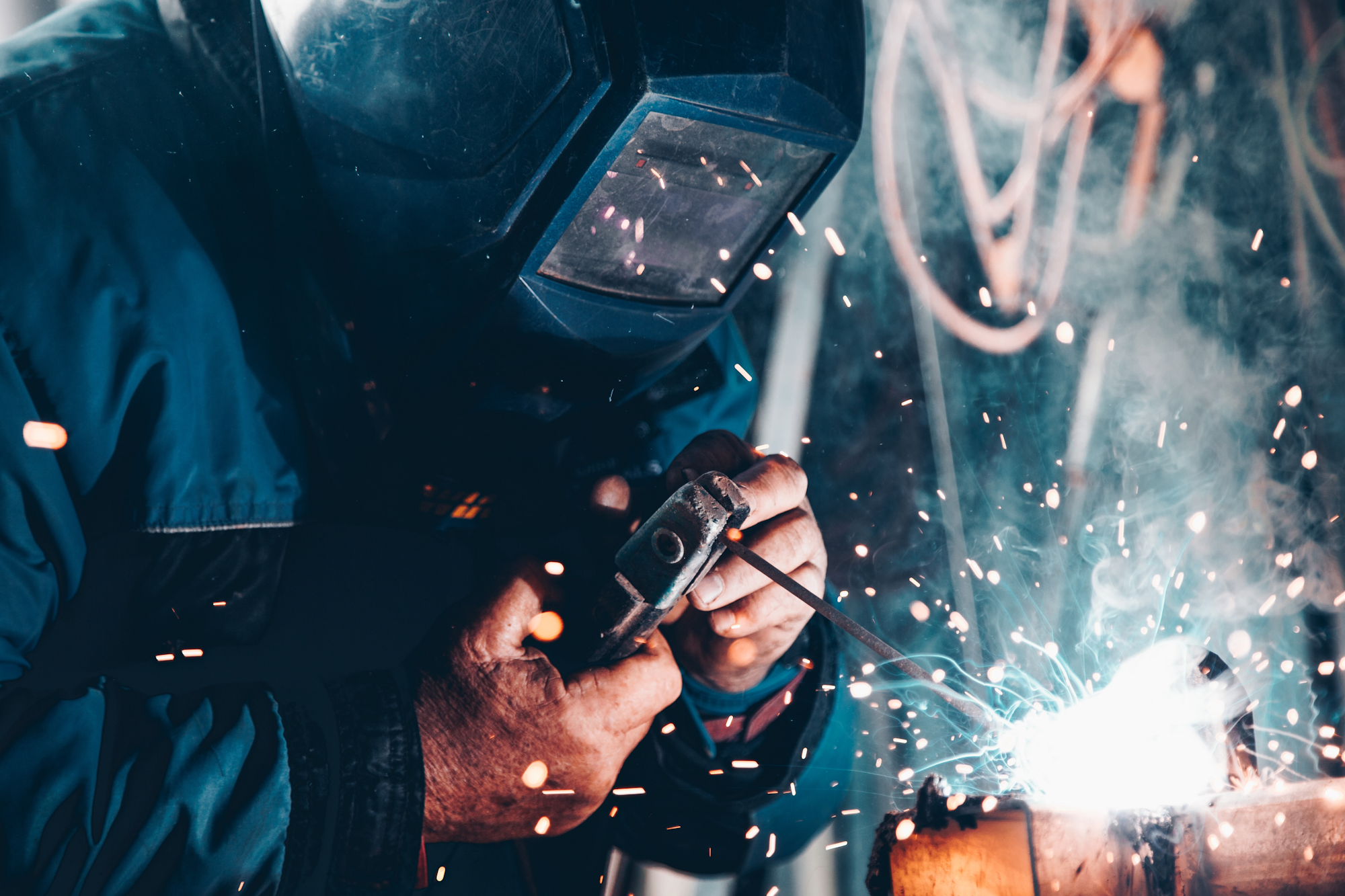
Rising costs of steel and aluminium are currently causing great concern in the construction industry. Here we look at the reasons why prices have risen so drastically since the beginning of 2020, and try to understand what the future holds.
Pandemic hits demand and production
When the coronavirus pandemic hit at the start of 2020, businesses globally scaled back their operations to match the reduced demand for products as countries went into lockdown. As workforces were decimated in attempts to impose social distancing and reduce the risk of spreading the virus, production dwindled. For a while, reduced production kept pace with reduced demand.
This was however a temporary lull in the storm. Industries running at reduced capacity were calling off materials from a supply chain that wasn’t being replenished. When end user demand began to rise again, idling production was unable to simultaneously match this demand and restock the supply chain.
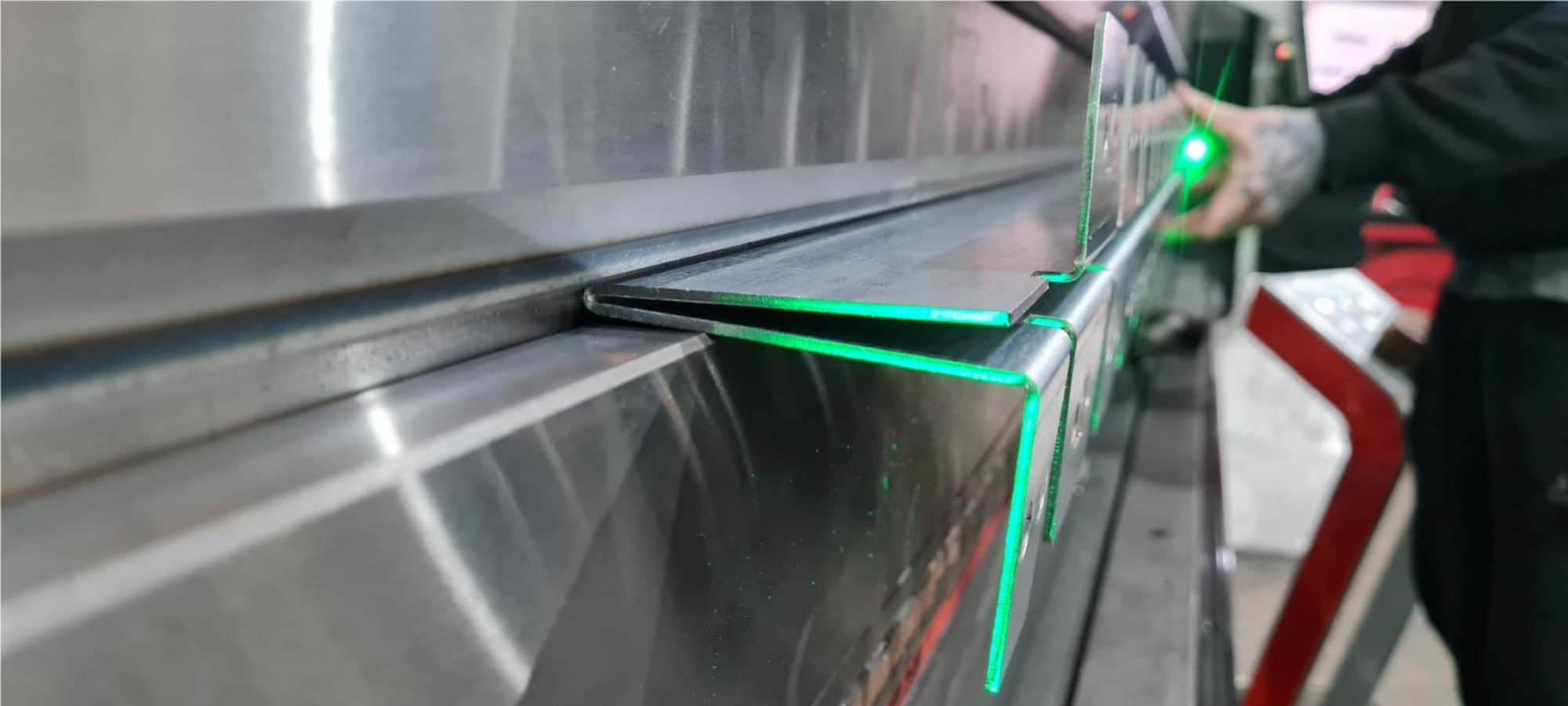
Raw materials prices increase
From March to December 2020, iron ore prices almost doubled, those of metallurgical coke rose by around 45% and scrap steel prices rose by about 70%.
As one of the world’s largest suppliers of steel, China’s exports were reduced due to a number of factors.
- They introduced a strong economic stimulus – at 6%, the highest since the Global Financial Crisis of 2007-08
- This saw massive increases for domestic demand; by Q3 2020, China’s steel export volumes had shrunk to a low not seen for many years
- They cancelled the 13% VAT rebate on exports which had been an incentive for mills to sell steel abroad
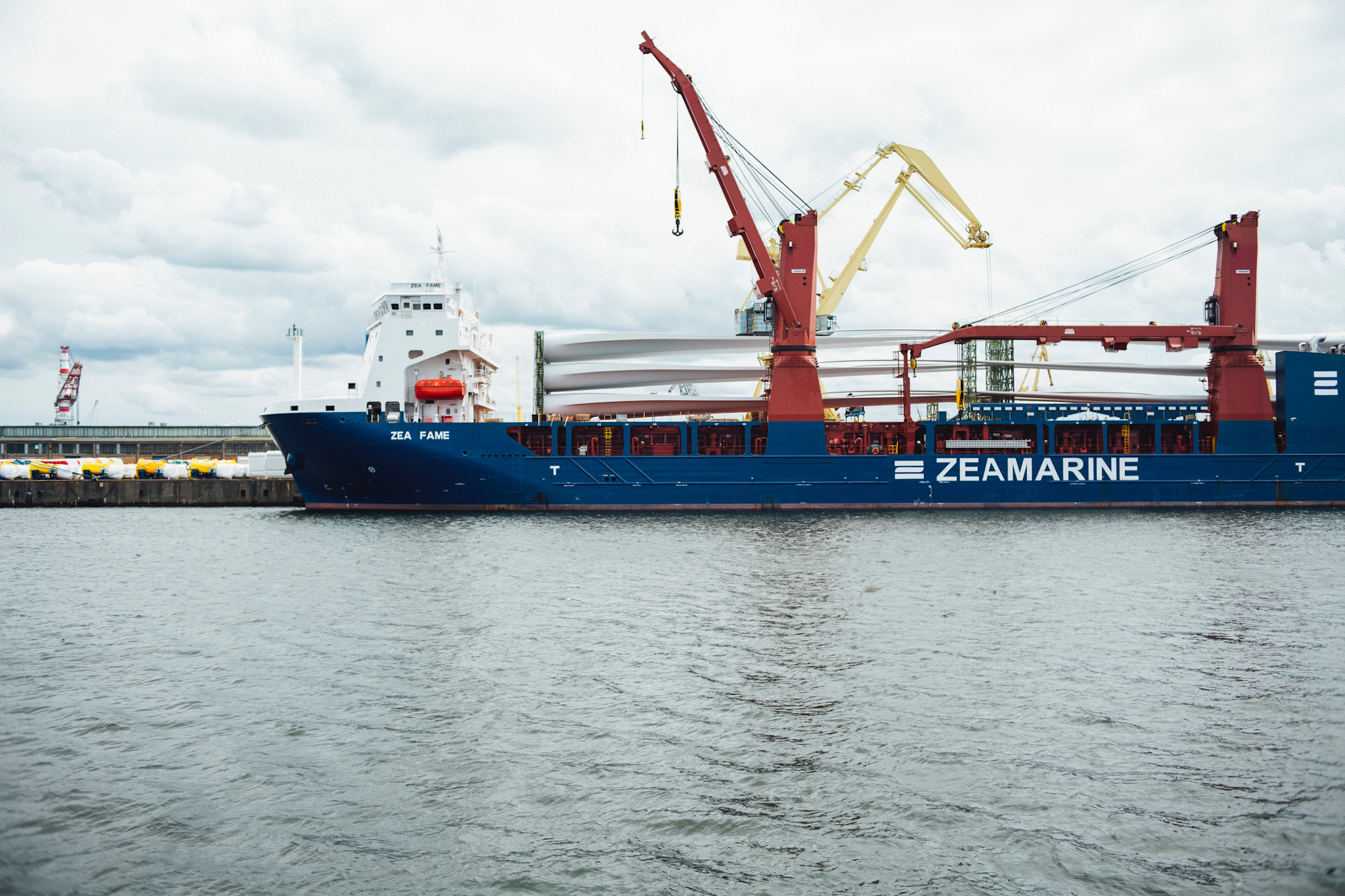
For the UK, post-Brexit tariff limits have also impacted on the availability and price of imported steel. With a pattern emerging of tariffs progressively rising during the course of each quarter, buyers have been tempted to bulk buy steel at the beginning of the quarter to avoid later price increases. Availability has been impacted as a result and this has driven further price increases.
Turning to aluminium, 2021 saw aluminium prices rocket by 40%, higher than any other traded metals. One of the factors behind this increase is political unrest in Guinea, West Africa, one of the world’s top producers of bauxite. Sold to China for processing, Guinean bauxite produces over half of the world’s aluminium, but a regime change in September 2021 has led to uncertainty over future supply with fears of sanctions being imposed by other nations.
Longstanding power interruptions in China have also negatively affected aluminium production. Tasked with meeting new and lower energy consumption targets by a world committed to climate change reduction, Inner Mongolia and Xinjiang have been forced to reduce production volumes. This has coincided with severe drought conditions in Yunnan, where hydroelectric is a major source of power supply.
Events in other world regions where bauxite is mined and processed have also contributed to this situation, including a strike in Canada by Rio Tinto smelting workers and Jamaica’s second-largest aluminium refinery being shut down indefinitely following a fire.
Future predictions
According to experts, the situation that saw steel prices rise disproportionately higher than costs is a once in a decade phenomenon that is unlikely to repeat itself again for a long time.
But market volatility has also been a contributory factor, and this is still a concern. Prices of some steel products have been held down at unsustainably low levels for so long that steel mills are now struggling to stay viable. Increases to ensure supply continuity in the future now look like a painful inevitability.
There is also the inseparable link between steel prices and energy costs. As Europe faces the probability of energy supply shortages and spiralling costs while the West places sanctions on Russia, it is unlikely that steel prices will escape unscathed.
Energy is also likely to affect the price of aluminium, but another factor is poised to influence the price of this metal – electric cars. With governments committed to phasing out internal combustion powered vehicles by the end of this decade and the popularity of these supposedly ‘green’ vehicles, the demand for aluminium (which is used far more extensively in electric vehicles than in their petrol or diesel equivalents is likely to drive prices further upwards.
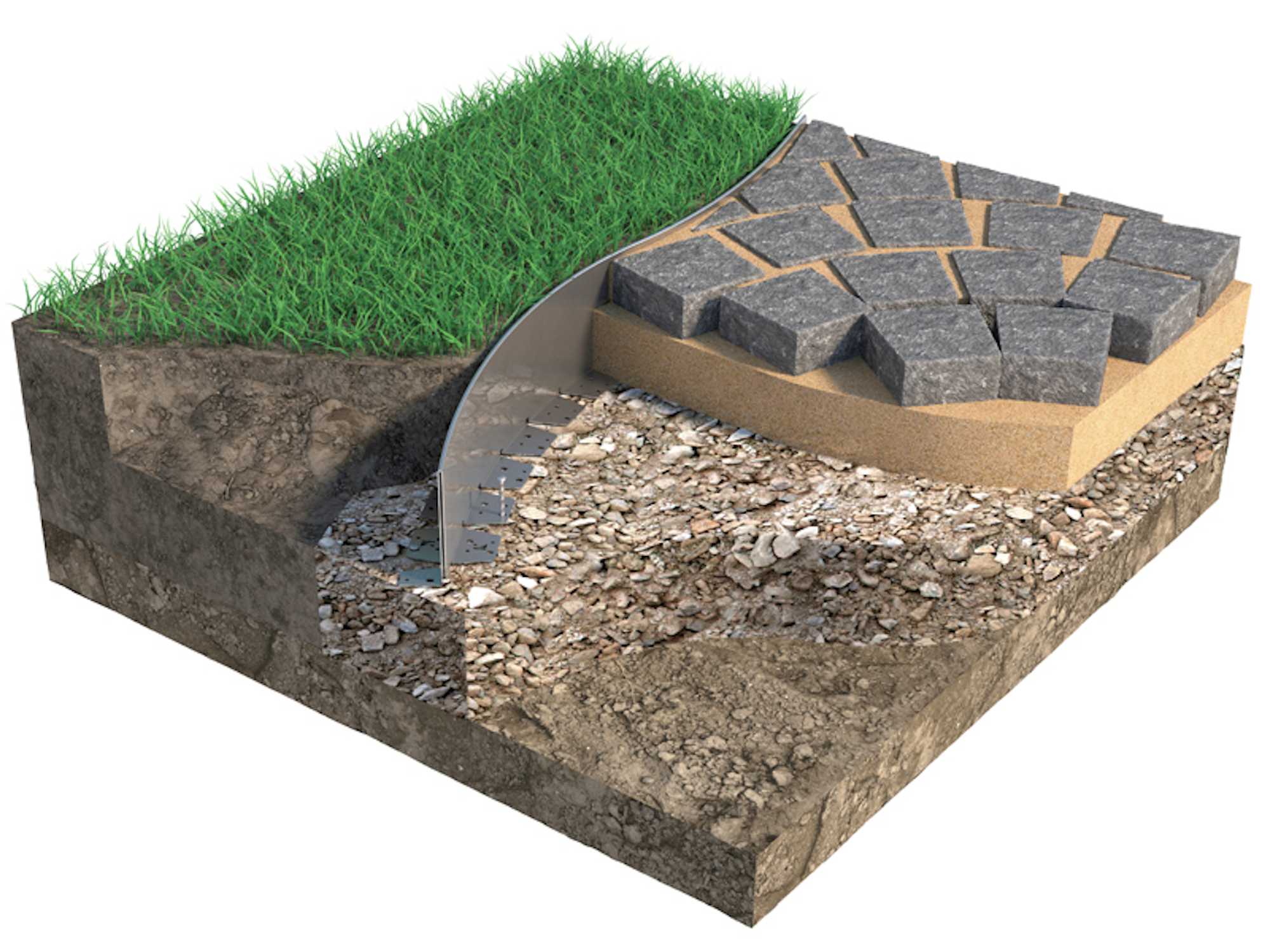
The good news?
The majority of Kinley's edging is manufactured in-house, which gives us more influence over our costs. It allows us to understand metal better and gives us more control and the ability to make things happen and happen fast. This has led to our products being made more efficiently, more economically, using less energy, more quickly and with a higher level of safety for our staff. As we continue to evolve, we aim to drive down lead times on both standard and bespoke products, by focussing on what we do and accelerating innovation in every way. And most importantly, striving to provide the best customer service for our customers.